干式壓縮成型工藝:高純粉末屬于貧瘠材料,不能用傳統工藝成型。首先,通過添加一定量的表面活性劑,改變粉末的表面性質,包括顆粒表面的吸附性質和粉末顆粒的形狀,從而降低超細粉末的團聚效應,使其均勻分布。增加潤滑劑減少顆粒之間及顆粒與模具表面的摩擦;加入黏合劑增強粉料的粘結強度。將粉體進行上述預處理后裝入模具,用壓機或專用干壓成型機以一定壓力和壓制方式使粉料成為致密坯體。成為可加工陶瓷
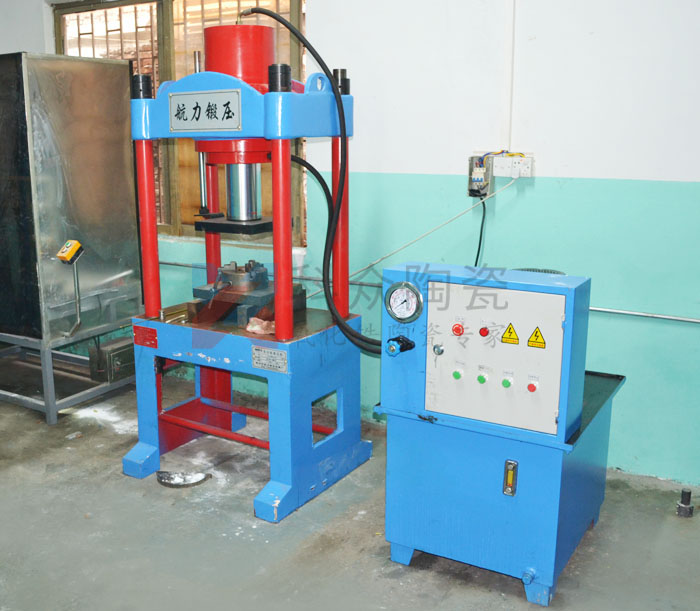
干壓成型機
下面就上述幾方面因素對干壓成型的影響分述如下:
A、模具的光潔度和配合情況:
干壓成型對模具質量要求較高,首先要求模具硬度達到一定的要求。由于氧化鋯穩定料的顆粒很細,流動性差,因而對模具的光潔度要求很高,若光潔度達不到要求,則干壓時影響料的流動,從而導致分層的出現。同時,若模具配合不好,間隙大,則由于氧化鋯粉料顆粒細,壓制時粉料會從模具間隙中流出,從而造成模具四周的粉料少,這樣壓制時四周就不能壓實,從而會因壓力傳遞不一致而出現分層,故對模具的配合要求較高。
B、成型壓力:
成型壓力在氧化鋯干壓成型過程中是較關鍵的,壓力太小和太大都不能壓制出理想的坯體。壓力太小,則燒后產品的密度小,產品收縮大,坯體壓實程度不夠容易出現分層;而壓力太大,坯體也容易出現裂紋、分層和脫模困難等現象。合適的成型壓力需要通過生產實踐來摸索。
C、加壓方式:
般干壓成型時加壓方式有兩種,一種是單面加壓,另一種是雙面加壓。當單面加壓時,則直接受壓的一端壓力大,出現明顯的壓力梯度,粉料的流動性越差,則坯體內出現的壓力差也就越大,越容易出現分層。雙面加壓時,坯體兩端直接受壓,因此兩端密度大,中間密度小,其壓力梯度的有效傳遞距離為單面加壓的一半,故坯體的密度比單面加壓要均勻得多。因此氧化鋯陶瓷干壓成型時宜采用雙面加壓的方式。
D、加壓速度和保壓時間:
加壓速度和保壓時間控制不好也會造成氧化鋯陶瓷坯體出現分層等缺陷。壓模下落的速度應緩慢一些,如加壓速度過快,則坯體中氣體不易排出,從而導致坯體出現分層,表面致密而中間松散,以及存在氣泡等現象。如保壓時間過短,則壓力還未傳到應有的深度時,外力就已卸掉,這樣坯體中氣體不易排出,就難以得到較為理想的坯體,會導致坯體出現分層以及存在氣泡等現象。同時保壓時間應均勻一致,否則會引起產品厚薄不均,造成廢品。
E、脫模方式和脫模速度:
干壓脫模時一般采用工具將坯體從模腔中頂出,脫模速度要均勻緩慢,如不注意會引起坯體開裂。實踐表明脫模時脫模工具要平整,否則會引起坯體受力不均而造成開裂??傊?,干壓成型和上述幾方面因素都有關系,要成型出理想的坯體,以上各方面都要控制好。
地址:http://www.lmgvip.cn/bangzhu/1451.html
本文“工業陶瓷干壓成型時應注意什么?”由科眾陶瓷編輯整理,修訂時間:2020-05-05 17:02:37
科眾陶瓷是專業的工業陶瓷加工生產廠家,可來圖來樣按需定制,陶瓷加工保證質量、交期準時!
- 上一頁:什么是氮化鋁陶瓷片?
- 下一頁:氧化鋯陶瓷管與氧化鋁陶瓷管具有哪些優勢?